Cut-throat competition in the industries requests that producers accomplish more with less time while keeping up high quality. Hardware that can multi-task can replace a few pieces. This mix can help dispense with ventures in the creation procedure.
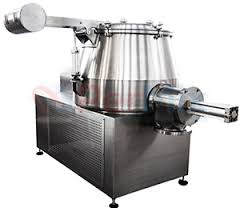
Multi-agitator mixers can do only this. They work by utilizing a few separate instigators and can without much of a stretch change gears for making a few unique products. This capacity of the high shear mixer with multi-agitator blades to deal with different sorts of products can help react to the requests of a continually evolving market.
A mixer that has a few fomenters that stay stationary inside the vessel is viewed as a multi-instigator mixer. These fomenters turn all alone tomahawks. This kind of development makes mixing exceptionally practical. Changes in configuration have made the magnetic mixer considerably more proficient and skilled. There are three separate instigators and each one is controlled independently.
The three wing grapple fomenter uses tender mixing and advances hub and spiral flow. This low shear fomenter uses a tender mixing procedure. Heat is scattered by keeping the batch moving inside the vessel by utilizing Teflon scrubbers which keep a layer from collecting within divider. The grapple is triangular formed to help keep the flow pulled toward the inside of the batch. Expansive batches particularly require such development of the stay fomenter. It is in steady movement to help the batch flowing with the goal that it is blended reliably.
It is adaptable since a few diverse sharp edge styles can be designed. The high speed powder mixer accomplishes standard conveyance of molecule size and enhances the quality of the last item. It decreases bigger particles with the goal that they can be appropriately scattered. When they are smaller they can be deteriorated by the high shear type mixer.
There are a few things that must be considered when settling on which sort of inline mixer is ideal. What force is expected to keep a sufficient flow in the vessel, the level of shear expected to blend legitimately and the material’s capacity to endure heat and shear should all be considered.